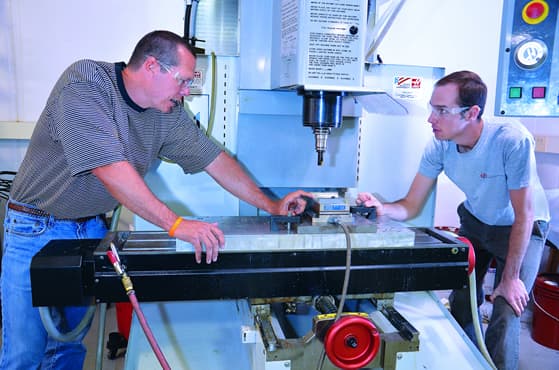
Through their research in developing advanced machining analytical models, Tony Schmitz and his students are bringing science to the art of high-speed manufacturing.
“We’re making manufacturing more efficient by applying a physics-based understanding of the processes involved,” said Schmitz, an associate professor of mechanical engineering and associate of the Center for Precision Metrology. “This is smart machining for use in intelligent manufacturing.”
The team has designed and built special test set ups in order to analyze and model machining processes. Model inputs include basic physical properties such as the force required to shear away the material being machined and the dynamic response of the cutting tool clamped in the spindle, as well as the process variables involved such as the cutting speed, feed rate and depth of the cut.
“We model the machining dynamics is order to select operating parameters that achieve maximized material removal rate during machining. This reduces cost,” Schmitz said. “For some hard-to-machine materials, the cutting speed must be relatively low to avoid prohibitive tool wear. In this case, we can take advantage of a phenomenon known as process damping.”
During machining, energy is input into the process in order to remove the required material, but this energy can also cause structural vibrations. These vibrations can limit the allowable depth of cut and, therefore, the material removal rate. At low speeds, however, interference between the cutting tool’s relief face and the machined surface can dissipate energy and enable increased depths of cut.
“There is a line between stable and unstable cutting,” stated Schmitz. “Process damping moves the line to deeper cuts. If we can model process damping, we can use this information to select the best machining conditions prior to performing a cut. This saves time and cost.”
As part of his thesis research, Ph.D. student Chris Tyler has developed special testing setups to measure the machining forces. This data is then used to create analytical process models. Tyler then does more testing to validate the accuracy of the models.
“So far we have worked with four different materials to identify their individual process damping characteristics,” Tyler said. “This involves working with various tool geometries and cutting conditions for each of the work piece materials.”
The testing involves first determining the frequency response (or dynamics) of the structure (the cutting tool clamped in the spindle) by tapping it with an instrumented hammer. Then through the different test setups, they identify the process model and select operating conditions that provide stable operation with maximized material removal rate.
The first test setup design used a single-degree-of-freedom flexure, which provided controllable and repeatable dynamics. The flexure leafs were 3.13 millimeter thick aluminum sheets. A steel sheet was used as the top platform to increase the mass of the flexible system. The entire system was fixed to the machine table using T-slot nuts to ensure a stiff connection. An accelerometer was also mounted to the flexure platform to provide in-process data for stability evaluation.
With this setup, the team was able to identify stability limits for various axial depth of cut-spindle speed combinations. With this information, they could calculate the process damping coefficients.
“Our whole goal is to develop stability load diagrams,” Tyler said. “These show the process damping limit for cutting speeds and depths of cut. Essentially this limit shows you where larges vibrations will occur, so you can then pick the optimum process variables for the greatest efficiency.”
This type of information is very valuable to process planners and machinists as they try to determine optimum machining conditions.
“The models show the limit between stable and unstable cutting with the addition of process damping,” Schmitz said. “With the model you don’t have to be overly conservative with expensive materials, but you can instead safely select deeper, more productive cuts.”
The process damping modeling work has gone very well. “We’ve been really pleased with this project,” stated Schmitz. “We have developed general models for process damping for several hard-to-machine materials, and we have been able to extend the models substantially in last few months.”